注塑行业解决方案
伴随着社会经济发展的直线上升,大众日用生活物资需求量越来越大,尤其对注塑制品的需求不断增加,对于整个注塑行业的发展也获得了爆发式增长。注塑行业属于典型的多品种小批量生产模式,产品规格多、工序冗杂,产能直接影响交期,对于注塑企业来说,整个生产及供应链体系必须与上游协同,才能够确保品质、交期的要求。随着市场竞争的加剧,注塑企业正在不断追求更精益化的管理以应对市场挑战,如何以合理的价格提供最佳质量的产品,有效地提升制造交付能力和成本管控能力成为了摆在企业面前的难题。
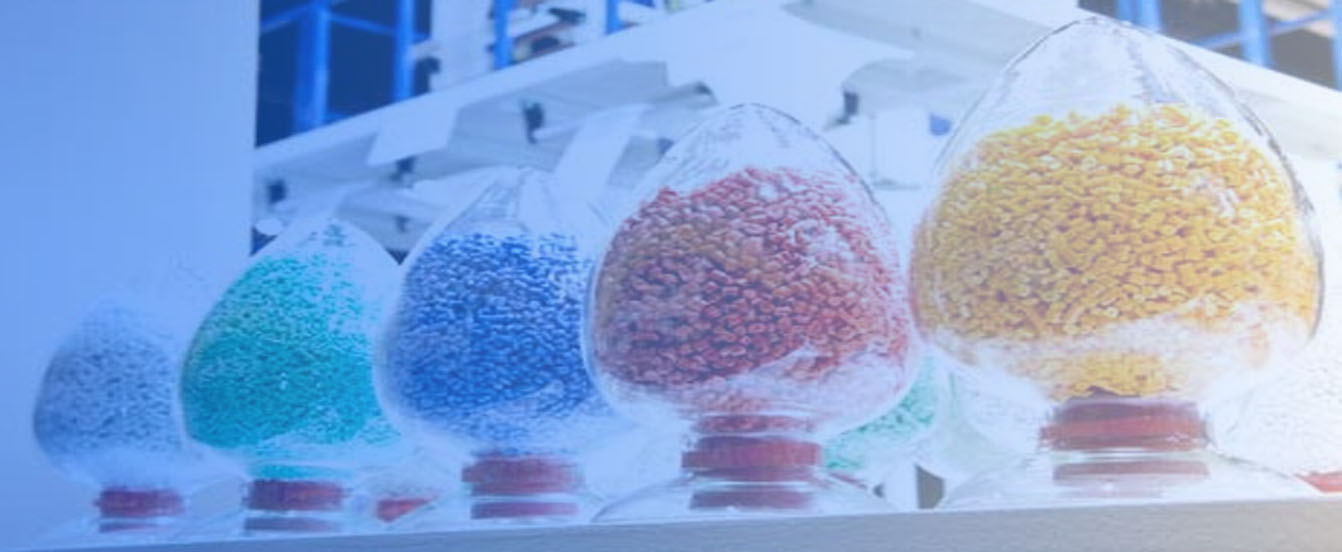
行业痛点






业务挑战
解决方案
从企业生产管理透明化、及时性、精细化、精益生产等管理方面出发,打通从设计研发到生产出货的各阶运作单元,实现由控制层、运营层到企业层的网络化、信息化集成,消除信息孤岛;以生产订单为主线,实现研发、工艺、生产、质量、设备、物料、营销的业务协同,实现产品全生命周期的信息化闭环以及全产业链可追溯;增强企业的灵活性和工作效率,提高企业核心竞争力。
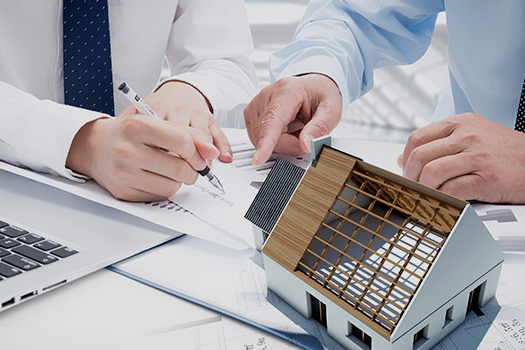
根据到料状态、模具状态、设备状态等生产准备信息,依据需求来源,基于生产资源齐套性,实现供应链生产计划协同联动,对生产计划排单到机台,实现排程科学化,极大的提高了设备利用率
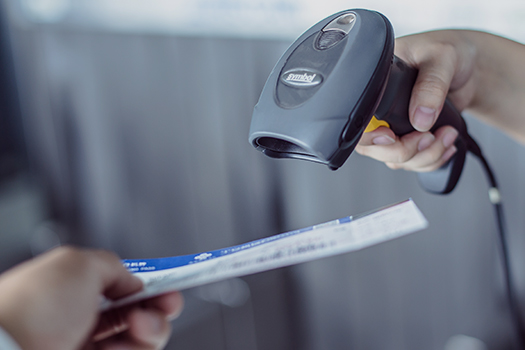
根据物料的特点及其属性制定企业内部的物料编码,对同种原材料或产品进行批次管理,采用先进先出的原则,控制物料的存放周期,减少呆滞物料报废的情况,通过PDA扫码进行出入库管理,同时自动生成ERP单据,完成记账工作,进一步提升效率。
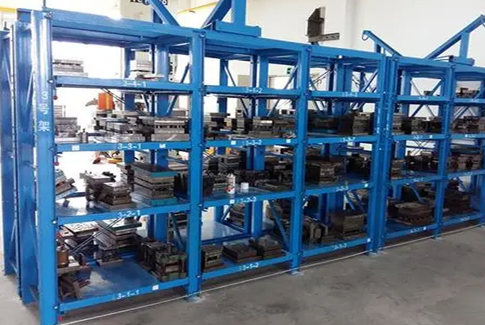
在线建立模具履历,实时监控模具的状态,闲置,离线,报废可视,出入库台账,管理出入库情况,寿命等可视化管理,自动预警,报废及时提醒,维修保养预警,状态实时追踪,对模具寿命进行预测性提醒,实现从模具入库、出库、维修、保养到报废的全生命周期管理
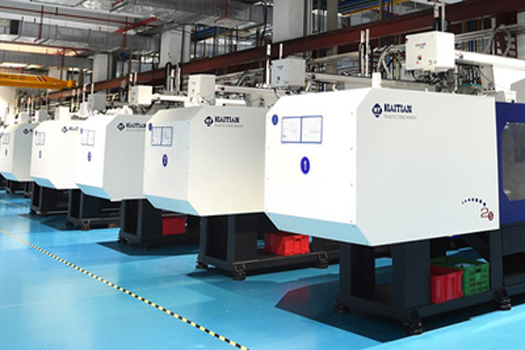
通过设备联网,实时获得设备状态、故障信息,及时处理,通过移动设备进行点检、保养、维修,全程记录和预警,实现预测性维护,灵活配置维保计划,减少损耗,实现设备的自动保养提示和性能评估,并为生产排程提供科学依据。
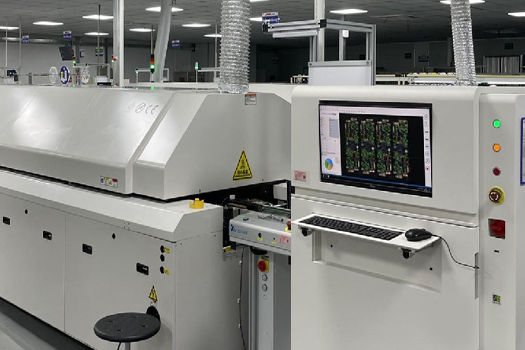
利用条码或RFID流程卡,结合工艺路线管控,控制前后工序流转,防止工序漏做、前后置颠倒,完工确认工时及数量,结合设备联网实时监控生产线各工序任务完成情况,对生产流程进行有效执行反馈,并对WIP在制品数据、质量信息进行实时监控预警,确保生产过程的顺畅进行。
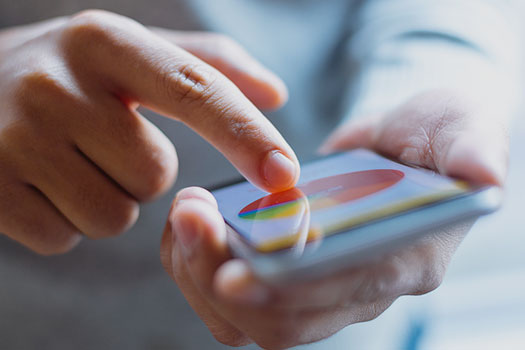
质量管理以预防为主为前提,实时控制为目标,首检、定时巡检、末检、成品入库检等贯穿整个生产流程,建立完善的质量检测和处理流程及工位作业指导体系。关键质量数据实时监控,异常及时多端报警,支持移动端质检,结果随时拍照上传,实时生产质量数据报告,便于分析改进。
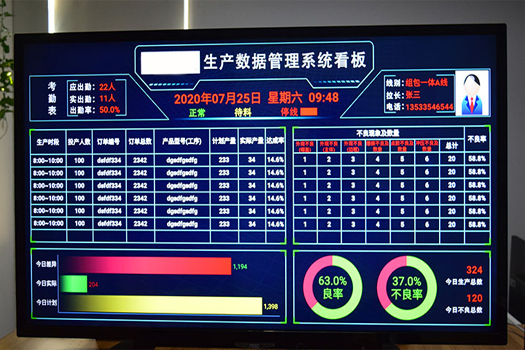
实时电子生产看板,工作中心看板,生产日看板,质量监控看板,设备监控看板,安灯监控看板等数据呈现,生产各类数据进行实时监控,统计分析, 方便管理者实时掌控企业运营现状,实现工厂透明化、可视化管理。
应用价值
相关产品
从数据收集、加工到数据分析、应用,实现生产、供应链、应用和其它元素的可视化,实现业务价值赋能,有效支撑科学化、智慧化决策
全新数字化协同管控方式,应用于车间派工、生产、设备、质检等各个场景
利用设备数据网关实时采集设备运行数据,并传输处理,针对现场设备进行全生命周期管理
管控从采购、领料、生产、仓储到发货及服务等工厂运营作业环节。
提供企业生产整体供需规划及不同层次的生产规划与控制相结合的排程方案,随时适应生产调度
以客户数据管理为核心,记录企业在市场营销和销售过程中和客户发生的各种状态交互行为,为后期的分析和决策提供支持。